Among the all structural Members the Design of Columns are very important yet the Design of Columns are much neglected. This importance of Structural nature of column is because if any other structural member say Beams or Slabs fails, it will cause only a local failure in that particular portion of the structure.
Whereas, failure of a column means that the of that particular column which has failed will have to be borne by the adjacent columns,hence it will give loads on the adjacent columns beyond their Design Limit. As due to this fact it may start a chain reaction of failures in columns and subsequently the whole structure may collapse. As in the Framed Structured Building that is in the modern day construction the Frames are formed by networks of Columns and Beams. Due to all this reason only even if vertical or Gravity loadings are considered the Design of Columns stands to be of much importance than any other structural Members.
A Column is a Structural Member which is vertical and axially loaded and subjected to Compressive forces, and having it’s Effective Length (Height) Three times greater than the least cross-sectional dimension of it self. To Satisfactorily Complete the
Design of Columns The Following Steps must followed.
STEP 1 :- Calculation of the Influence Area for Design of Columns :
The first step is to find out the Influence Area of the Column to be Designed. The Influence Area of a column is the area of which load is being transferred to the column to be designed for. For this purpose in a framed structure small and medium building the design of column is done for the column whose Influence Area is the largest hence the load coming on the column will be so the greater of the any other column in that building hence all the other column having lesser Influence Area hence lesser Loads if provided with the same Designed parameters that required for the column having largest Influence Area, then the whole Structure will automatically become safe against the Loads.
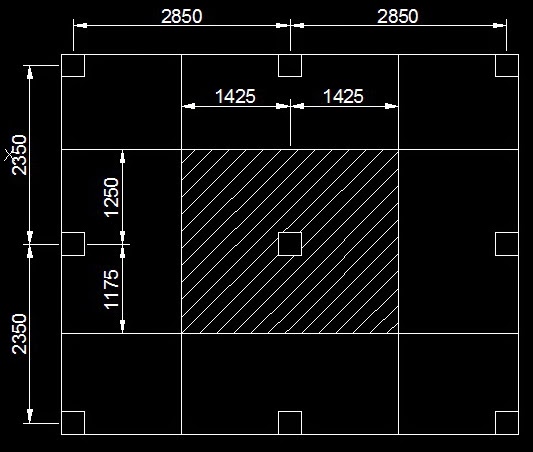 |
DETERMINATION OF INFLUENCE AREAS FOR LOAD DISTRIBUTION ON COLUMNS |
STEP 2:- Calculation of the Loads Coming on Columns from the Influence Area :
In this step the Load Calculation is being done. This is done by calculating all the loads acting within the influence area.
The Loads acting are broadly classified as Dead Load (DL) and Live Load (LL). Dead Loads are the load of objects which cannot be moved from on place to another like the loads of Brick Work, Beams, Slabs etc. and the Live Loads are the loads coming from movable objects such as Humans, Chair, Table etc.
Thus We Need to Calculate the Dead Loads as well as Live Loads within the Influence Area, these are as follows in the general case of a Building :-
I. Due to weight of Slab [25000 N/m3 ]
II. Due to weight of Floor Finish [500 N/m2]
III. Due to weight of Brick Masonry [19200 N/m3]
IV. Due to weight of Beam [25000 N/m3]
V. Due to weight of Self Weight of Column [25000 N/m3]
B) Live Load :
It depends upon the Nature of the Structure, and it values for different structural nature are given in the concerned Code of Practice, like in India these are given in I.S.: 875-Part II.
For Residential Buildings it is generally considered @ 2KN/m2 = 2000 N/m2
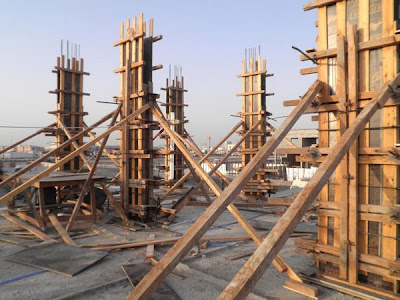 |
COLUMN FORM WORK OF BUILDING |
Now after correct calculation of above loads the Total Load is Calculated by,
Total Load on each floor = Dead Load + Live Load
Now this the actual load which will be acting on column for each floor, now if the building say 5 storied, then just multiply the value with the nos. of floors, like for five storied building multiply the Total Load on each story with 5.
Now thus the Total load acting on column at Column Base is Obtained and it is denoted with ‘P’.
Hence P= Total Load on each Floor X Nos. of Stories = (Dead Load + Live Load) X Nos. of Stories.
Now we shall move to the actual Designing to determine suitable Column sections and its Reinforcements so that the above load is safely resisted by the column Designed.
It can be done by Three main Methods of Design : a) Working Stress Method b) Ultimate Load Method and c) Limit State Method.
The Modern Practice is to use Limit State Method for all types of Designing, Hence I’ll discuss here the Limit State Method Of Design Of Columns.
STEP 3 :-Finding The Gross Cross-Sectional Area Required For The Design of Columns :
This is the one of the most important and main step of the Design of Columns.
First in the Limit State Method of Design of Columns we must increase the load acting on the column with a Load Factor so that if there will be any accidental increase of loads the column will be still safe to resist the load without a failure. The Factor of Safety for Dead Load + Live Load Combination is 1.5, hence we must multiply the load action on column (P) with the 1.5 to obtain the Ultimate Load that is the Factored Load of the Column that is Pu.
Hence Factored Load, Pu = 1.5 X P
For Design we will work with this value of load.
Now before going on I’m here to say that I will design according to the Code Of Practice of I.S.: 456-2000
The Ultimate Load of a Column is given by,
Pu = 0.4.fck.Ac + 0.67.fy.Asc [Equation I]
Where, Pu = Ultimate Load of the Column in N/mm2
fck= Yield Strength of Concrete in N/mm2
Ac = Area of Concrete (Cross-Sectional Area) of Column in mm2
fy = Yield Strength Of Steel in N/mm2
Asc= Area of Steel (Cross-Sectional Area) in Column in mm2
Now the column consists of Concrete and as well as Steel in the form of Reinforcements hence the Total Cross-Sectional Area of Column is made of Area of Concrete and Area of Steel.
The Total Cross-Sectional area of Column can be also termed as Gross Cross-Sectional Area of Column and it’s denoted by Ag.
Hence, Gross Cross-Sectional Area of Column = C/S Area of Concrete + C/S Area of Steel
Therefore, Ag = Ac + Asc
And hence, Ac = Ag – Asc
Now putting the above obtained value in the original equation (Equation I) we get,
Pu = 0.4.fck.(Ag-Asc) + 0.67.fy.Asc [Equation II]
Now Assume the Percentage of Steel you want to use ranging anywhere from 0.8% to 6% with Respect to Gross Cross-Sectional Area of the Column (Ag). Say Assuming Steel as 1% of Ag it means Area of Steel Asc = 1% of Ag = 0.01Ag
The higher will be the percentage of steel used the lower will be Ag and thus lesser will be the cross-sectional dimension of the column. But the as the Price of Steel is very high as compared to the Concrete hence it is desirable to use as less as steel possible to make the structure economical, again if the percentage of steel is lowered then the Ag will increase at higher rate, about 30% with decrease of just 1% of steel and so each lateral dimension of the column will increase and will cause a gigantic section to be provided to resist the load. Therefore both the factors are to be considered depending upon the amount of loading.
My suggestion is to use the following Percentage of steel for the Design of Column, Which I’ve found to be effective and to produce economical and safe section of Column.
Loading (Pu) in N Percentage Of Steel for Satisfactory Design
Below 250000 ——————————————–0.8%
250,000 to 500,000 ————————————–1.0%
500,000 to 750,000 ————————————–1.5%
750,000 to 1000,000 ————————————-2.0%
1000,000 to 1500,000 ———————————–2.5%
1500,000 to 2000,000 ———————————–3.0%
And so on, with increase of each 250,000 N increasing the Percentage of Steel as 0.5%.
Now input the value of the Asc in the form of Ag in the Equation I. For example suppose 1% Steel is used then the equation will be like the one below :-
Pu = 0.4.fck.(Ag-0.01Ag) + 0.67.fy.0.01Ag
Therefore, if we know the Grade of Concrete and Grade of Steel to be used and Factored Load coming on the Column and Assuming the Percentage of steel required appropriately then we can Very Easily Calculate the Gross-Sectional Area (Ag) of the Column required from the above form of the equation.
Now as the Ag is obtained thus the Lateral Dimensions of the Column that are the sides of the column can be easily determined.
The Ag or Gross-Sectional Area of the Column means that it is the product of the two lateral sides of a column [i.e. Breadth (b) X Depth (D)], hence reversely knowing the Ag we can determine the Lateral Dimensions.
For making a Square Section just Determine the Root Value of the Ag. Like if the Value of Ag is 62500 mm2Then considering square section of a column we can get each side
Also Rectangular Column Sections Can be made by using different proportion say b : D = 1 : 2 , Hence D=2b , Therefore, Ag = b X D = b X 2b = 2b2 or b=
Hence D can be also determined as D=2b after Calculating the b.
Most of the times after calculating the sides of a column it will give results such as 196.51mm or 323.62 etc. values, which practically cannot be provided at field, hence we must increase those values to the nearest greater multiple of 25mm (i.e. 1 inch). For examples a value of 196.51mm may be increased to 200mm or 225mm or 250 mm even, and a value of 323.62mm may be increased to 350mm. more it will be increased the more it will be safer, but it is uneconomical to increase by a very high amount, it should not be increased more than by 75mm to consider the economical factor.
STEP 4 : Check For Long/Short Columns:
Depending upon the ratio of Effective Length to the Least Lateral Dimension of a column, a column may be classified as Long Column and Short Column. If the value of this ratio is less than 12 then it’s called as a short column and if the value is more than 12 then it’s called as a Long Column. A short column mainly fails by direct compression and has a lesser chance of failure by buckling. And in the case of a long column the failure mainly occurs due to the buckling alone. Long column being slender, that is being thin like stick as compared with its length it grows a tendency to get bend by deviating from its vertical axis under the action of loads. Due to this tendency of long column to get buckled (bend) a long column of all same properties and dimensions that of a short column will be able to carry much lesser load safely than that of the short column.
Suppose a 400mmx400mm short column can take a load of 1000KN , then a long column of 400mmx400mm having same grade of concrete, same amount of reinforcement and same workmanship will be able to carry a lesser load like say about 800KN only, hence we get a loss of 200KN which is 20% loss of load carrying capacity. So the above formula used in Step 3 holds good only for the Short Column. For using it in long column a little modification is needed, which I will update it later when I will get hands on this article again. For now let us concentrate on Short Column. First of all we need to find out the effective length of a column, which can be obtained by multiplying a factor with the actual unsupported length of the column. The factor depends upon the end condition of the column. In most general cases we use a Both End Fixed Column for which The Factor is 0.65.
Therefore, Effective Length = Effective Length Factor (0.65) x Unsupported Length (l). suppose a column has a unsupported length of 2.7m = 2700mm, hence the effective length will be lef = 0.65×2700 = 1755mm. Least lateral dimension means the shorter of the two dimensions of column that is length and breadth. But in case of a circular column as there is only diameter, hence we will use the diameter.
Suppose a column is of 400mmx200mm section and has an unsupported length of 2700mm, then the Ration of Effective length t the Least Lateral Dimension will be as follows :-
(Effective Length/Least Lateral Dimension) = (lef/b) = (1755/200) = 8.775 which is less than 12 and hence is a Short Column.
STEP 5 Check For Eccentricity for Design of Columns :
Eccentricity means deviating from the true axis. Thus an Eccentric Load refers to a load which is not acting through the line of the axis of the column in case of column design. The eccentric load cause the column to bend towards the eccentricity of the loading and hence generates a bending moment in the column. In case of eccentric loading we have to design the column for both the Direct Compression and also for the bending moment also. Practically all columns are eccentric to some extent which may vary from few millimetres to few centimetres. In practical field it is almost impossible to make a perfectly axially loaded column, as a reason we have to consider a certain value of eccentricity for safety even though if we are designing for a axially loaded column. The conditions of considering eccentricity and its value may differ from code to code according to the country.
Here I will tell you what I.S. : 456-2000 says. According to it the eccentricity which we have to consider for design must be taken as the greater of the followings :-
i) 20mm.
ii) (lef/500) + (b/30)
Where,
lef = Effective Length of the Column
b = Lateral Dimension of the Column (We have to calculate two separate values for two sides in case of rectangular column)
Permissible Eccentricity :- 0.05b where b is the dimension of a side of a column, we have to check for two sides separately in case of rectangular column.
The Permissible eccentricity must be greater than or equal to the actual eccentricity of the column. Or else we have to design it for bending also.
STEP 6 :-Calculating The Area Of Steel Required for Design of Columns :
Now the Area of Steel Required Asc is to be calculated from the Ag as the predetermined percentage of Ag. For example if the Gross-Sectional Area of the Column is 78600 mm2and at the starting of calculation of Ag it was assumed that 1% Steel is used then we get,
Asc = 1% of Ag = 0.01Ag = 0.01 X 78600 = 786 mm2
Now we shall provide such amount of Reinforcements that the Cross-Sectional Area of the Reinforcement provided is Equal to or Greater than the Cross-Sectional Area of Steel required above.
Hence in the above case we shall Provide 4 Nos. of 16mm Diameter Bars
Hence, The Actual Area of Steel Provided,
Hence the Area of Steel Provided is Greater than Area Of Steel Required, Hence the Structure will be Safe.
NOTE : The minimum of 4 Nos. of Bars to be provided at the four corners of a rectangular or Square Columns and minimum diameter of Bars that to be used is 12mm Diameter. Hence 4 Nos. of 12mm Diameter Bars are must in any Columns irrespective of their necessities.
STEP 7 :-Determining The Diameter and Spacing Of The Lateral Ties for Design of Columns:
In this step we will Determine the Diameter and the Spacing of the Lateral Ties or Transverse Links or Binders.
The Diameter of the Ties shall not be lesser than the Greatest of the following two values
- 6mm
- 1/4th of the Diameter of the Largest Diameter Bar
For an example if a Column has 16mm and 20mm both types of bar as Longitudinal Bars or main Reinforcement then 1/4th of 20mm = 5mm Hence we shall provide 6mm diameter Ties.
The Spacing of Ties shall not exceed the least of the followings three values
- Least Lateral Dimension
- 16 Times of the Diameter of the Smallest Diameter Longitudinal Bar
- 48 Times of the Diameter of Ties
For an example A Column of 250mm X 350mm Dimension having 20mm and 16mm Diameter Longitudinal Bars and 6mm Diameter Ties we get,
- Least Lateral Dimension = 250mm
- 16 Times of the Diameter of the Smallest Diameter Longitudinal Bar = 16 X 16 = 256mm
- 48 Times of the Diameter of Ties = 48 X 6 = 288mm
Hence Provide 5mm Diameter Ties @ 250mm C/C
[In this case our objective is to minimize the value to reduce the spacing and to make the structure more stable, hence we shall take least value and suitably in a multiple of 25mm]
If you like this Article then I am sure you will like the following well researched articles too, come on check them out also